[columns_row width=”two-thirds-and-third”]
[column]
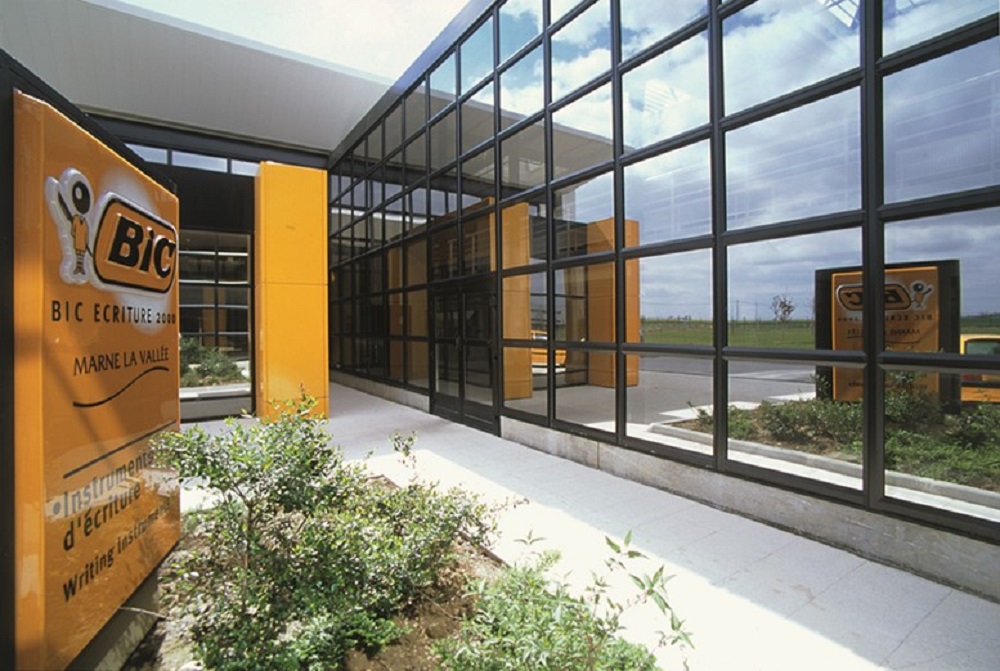
@BIC
The BIC factories in Vannes and Montévrain waited for the release of ISO 9001:2015 before certifying the quality management system. The Montévrain factory has also chosen the 2015 version of ISO 14001 to renew certification for its environmental management system. Interview with the project manager and two factory directors about the certification process.
Why did you wait for the 2015 version before applying for ISO 9001 certification?
Philippe Caré: “The documentary requirements in the 2008 version were slightly at odds with the BIC Group’s organizational culture. That is why we put our certification plans on the back burner for a year, so that we could work in keeping with the 2015 version, which is more attuned to our performance culture. Documentation must only be useful for the company and capable of creating value. Our teamwork played a key role in setting up a simple and ingenious system that makes everyone face up to their responsibilities.”
As for the Montévrain site, why did you decide to pursue ISO 9001:2015 and ISO 14001:2015 certification at the same time?
PC: “First of all, top management clearly wanted our Group to incorporate both systems (which concern all our activities) to significantly improve the joint work of all the services.
When defining the basis for our quality and environmental management system (QEMS), which is truly integrated into the different phases of the system, we identified the major operations of all our processes that supported the development of our quality risk management and environmental analysis. That is how our two certifications are integrated, and not only according to an identical document base containing the points that ISO 14001 and ISO 9001 have in common. ”
How did you manage to introduce the new management system?
PC: “It should be pointed out that we did not give operations and management a ready-made system. We did not believe in having two factory directors, advised by a quality expert, imposing a new system on the entire workforce. Everyone took part in building the new system, which naturally facilitated the system’s uptake. The other ground rule that we had established was that we would not tack a new system onto the legacy system. Therefore, I identified all the tried-and-tested elements of our previous management system that we could include in the QEMS that we were busy implementing.
In terms of the technical side of the certification process, we initially identified all the internal and external interested parties, as well as their needs, expectations and requirements. Then we described the aims of each of our business activities and defined the associated processes. Finally, we created a real on-the-ground communication campaign to ensure that employees at every level of the company understood and were convinced by the approach.
Our aim now for both factories is that ultimately we no longer have to prepare for an audit and can instead allow the audit to take its natural course and present our day-to-day operations to the auditor.”
After hearing the views of the project manager who sees himself as a facilitator rather than a quality manager, now it is time to ask the two factory directors for their thoughts on the management-based approach to certification.
As factory managers, how do you view ISO 9001?
Thierry Aupetit: “Although we are used to the auditing process, since some of our products are certified to the NF Environnement standard, this audit is beyond comparison. ISO 9001 taught us how to define the scope of each process, identify the missing links and eliminate non-value added tasks in an effort to build a system relating to continual improvement that is as simple as possible to avoid the pitfall of documenting everything and anything. I also enjoyed the concept of management-based control, which allows indicators to be aligned with our opportunities for improvement, not only performance indicators but also management indicators for viewing progress. ”
Emmanuel Barthelemy: “Let’s not forget that we already had a continual improvement culture at the site with ISO 14001. This approach paints a clear picture of BIC’s industrial culture and provides an excellent fit with the ISO 9001:2015 process. For example, our process incident records (PIRs) drive the approach, which is essential for naturally sustaining our system. There was no point using a short-lived solution to achieve certification without thinking about the long term. Our QEMS has improved communication between the departments for its implementation and that will continue in the future. For those of us whose work requires micron precision, it was vital to continue clearing up any uncertainties, and in that respect the ISO 9001:2015 process was extremely rewarding.
Another aspect is that our strong longstanding verbal culture was capable of changing in order to formalize the strict essentials. This means that we can retain the positive side of our legacy and incorporate the favourable improvements inherent in ISO.”
How did you engage your employees with this new approach?
EB: “We are primarily a family-run company, and that is our organizational culture. I know each and every person in operations. Therefore, I took the time to do the rounds and explain the importance and value of ISO 9001 to everyone, starting with the department managers and ending with middle management and sometimes the operations staff.”
TA: “We were already in the habit of holding half-yearly briefing sessions to address such topics as safety, quality, organization and operations. Prior to the audit, we explained the new certification during one of those sessions.”
[/column]
[column]
[button content=”ISO 9001 version 2015″ color=”yellow” text=”black” url=”http://www.boutique-certification.afnor.org/certification/certification-iso-9001″ openin=”_blank”]
[button content=”ISO 14001 version 2015″ color=”yellow” text=”black” url=”http://www.boutique-certification.afnor.org/certification/certification-iso-14001-management-de-l-environnement” openin=”_blank”]
[/column]
[/columns_row]