[columns_row width=”two-thirds-and-third”]
[column]
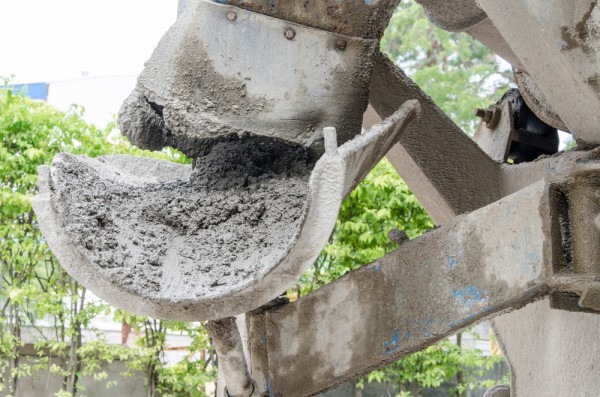
©Shutterstock/CoolKengzz
Less pollution and higher margins, the winning combination offered by ISO 50001 certification. And an invaluable asset in cement manufacturing. As illustrated in this interview with Tijani El Babor, at Ciments du Maroc which has a plant at Marrakech, the host city of COP 22.
In order to reduce our carbon footprint and our production costs. The cement industry is extremely energy-intensive. To produce cement you have to heat raw materials at a very high temperature (1,500°C) then crush them very finely, operations which use significant quantities of energy, both mechanical and thermal. Each tonne of cement produced requires one hundred litres of fuel and several hundred kilowatt hours of electricity, and releases on average 900 kg of CO2 into the atmosphere. A manufacturing process that pollutes and is also very costly for the company!
What method did you employ?
Ciments du Maroc has its own sustainable development policy which is divided into 7 axes, including health, safety, human rights and of course energy. We therefore already met several ISO 50001 criteria, but we needed to formalize our approach. We started by selecting the first site we wanted to get certified. In fact we chose the Aït Baha site near Agadir, the most modern of our plants, to set an example and drive the project forward. In addition to its centralized technical management systems, this plant has a solar thermal system which reduces dependency on fossil fuels and a cogeneration facility which recovers the heat generated during firing at 1,500°C.
What tools do you deploy?
Formation of an energy team comprising representatives of all interested parties, and establishment of well managed processes in order to properly structure the approach. From there, we put in place appropriate indicators and scoreboards for monitoring our energy consumption. The employees are very much involved. When we presented our monthly energy bill to them everyone knew already that it was very high, but nobody expected amounts like those! It therefore made a great deal of sense to reduce our energy consumption, especially in terms of fossil fuels given that Morocco itself has no fossil fuel resources.
What are the results achieved?
Month after month we are seeing our consumption fall. Our production costs go down and our margins increase! Our employees are routinely informed of the results. Before ISO 50001, the initiatives launched had already reduced our energy consumption, but the standard provided us with a structure for our document management, our organizational system and our communication. This has had significant effects and involves the entire workforce. Although return on investment is difficult to evaluate, our advances are tangible and we are achieving our goal of reducing our energy consumption and, within this scope, reducing our reliance on fossil fuels.
What are the next steps?
We adopt a continual improvement approach and aim to find synergies with the environmental issues described in ISO 14001. The Aït Baha plant obtained ISO 50001 certification in 2014 thereby becoming the first cement manufacturing facility in the country to hold the certification. Now we want to continue this progress and are looking at extending the Aït Baha exercise to our other sites, building on our experience and best practices. The key to success? Having the determination to commit and involving the company at all levels in order to accelerate deployment, gather ideas and communicate on actions and their results.
Interview with Tijani El Babor, head of Environment and Performance at Ciments du Maroc.
[button content=”More about AFNOR group and energy…” color=”yellow” text=”black” url=”http://www.afnor.org/en/insights/energies/” openin=”_blank”]
[/column]
[column]
[/column]
[/columns_row]