Certification is good. But factoring in numerous standards at once for numerous sites and sometimes numerous countries can soon become a headache! Don’t panic. Here are our tips with real-life examples.
Pandora’s box or Herculean task? When various certification standards meet various production sites, countries and business units within the same company, it’s enough to confuse anybody. With quality, security, the environment and sector-specific standards, the QHSE Manager – formerly QSE Manager and once just a simple quality manager – can easily drown amid the myriad items to certify and letters to assign to functions!
However, there is real benefit in covering multiple areas with the one exercise and targeting certification scope that extends beyond any specific place or activity. “You save both human and financial resources by combining audits with yearly sampling“, says Pierrick Bouchard, Key Accounts Sales Manager at AFNOR Certification (see box below).
Multi-site certification: establishing a network of correspondents
Keen to inspire widespread confidence, many companies have methodically – and successfully – taken the plunge! Let’s take Ugitech, a company in the Schmolz und Bickenbach group which specializes in the manufacture of alloy and stainless steel long products. Their wires and rods can be found, inter alia, in the automotive, aeronautical, medical, construction and nuclear sectors. The six France-based production sites have varied certification in different areas, including: ISO 9001 and ISO 14001, EN 9100, EN 9120, ISO 13485, IATF 16949 and ISO 50001. However, a small team is enough to manage the entire quality policy. How? With a unified system.
“If we can do more, we can do less“, says Olivier Martel, QMS (Quality Management System) Operational Manager. “We began by rolling out a network of 28 QMS correspondents at each of our sites, for each of our divisions. Each takes charge of a specific aspect, from purchasing to production, computer systems, etc. At head office, the central QMS department analyses and interprets the standards and distributes their requirements based on areas of expertise. We train each correspondent in the requirements for their sector.”
Multiple certification: levelling up
In practical terms, correspondents only take charge of the requirements for their own scope of activity. However, this entails a levelling up as they are asked to apply the most restrictive provisions in all areas. For example, the automotive standard is significantly more demanding than the others in the fight against counterfeiting. Thus, the automotive rules apply to the whole group purchasing and production chain by default. “And our clients in the aeronautical, nuclear and medical sectors are thrilled to see that we are going above and beyond the sectoral requirements!” says Martel with pride. This may be true but what is the answer in the case of diverging or even contradictory components for different standards? “We factor in these specific requirements on a case-by-case basis in the production chain – for example in the works order to keep a common thread for as long as possible” says Martel.
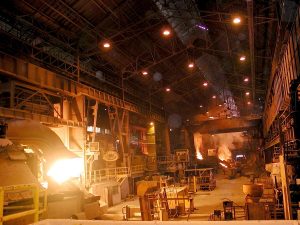
©Getty Images, DR
Once in place, this structure offers substantial time and financial savings. It’s advantageous in the way it synchronizes everything. Instead of multiple audits with oft-overlapping foundations, just one is organized. But this is not just any audit. Over a period of almost three weeks, six auditors analyze all company processes, which amounts to 54 audit days in one go. This single system also makes it easier to get to grips with the new guidelines and standards. “If we wanted to get ISO 19443 (quality system applied to the nuclear supply chain) or ISO 45001 (occupational health and safety) certification, we would simply need to study and compare it with what we are already doing. Any additional missing requirements would then be tackled by each of our QMS correspondents and members of the departments involved“, explains Martel.
Multi-country certification: synchronizing the first years
The synchronization process with Eurenco is coming to an end. Specialized in powders and explosives, this French chemistry company, which supplies defense players and additives for diesel engines, has two sites in France, one in Belgium and one in Sweden. “Each site worked with a different certification body, to the extent that the first years of their ISO 9001 standard never matched up“, recalls Jacky Jault of her arrival in the Quality Department in 2014.
To put things in order, the manager first decided to launch a call for tender to select a single body for all geographical sites and all standards. AFNOR Certification landed this contract in 2015. In parallel, a major employee awareness campaign was launched to underline the customer focus which must guide all company actions as part of the ISO 9001 standard and the process redesign. Getting all group teams on board with the process was one of the priorities.
“As the renewal dates came up, AFNOR Certification took over the ISO 9001 certificates for each site, organizing changeover audits if necessary to extend the validity period until everything is aligned in 2019“, says Jérôme Aragain, Manager of the joint QHSE standard, the internal audit program and the certification process. “This major upheaval was also an opportunity to switch to the 2015 version of the standard (the only recognized version now which replaces certificates based on previous versions) and extend the ISO 14001 certification to all the sites“, he continues. The next step is factoring in ISO 45001, which already forms part of the three-year roadmap.
It’s all about organization and method. Not yet there? Your certification body will be flexible and do all it can to find an all-purpose solution: a bilingual or even trilingual auditor with expertise in numerous standards and regions. But the unwavering support of senior management is always a prerequisite.
“For companies, there’s everything to play for”
Why begin a multi-certification process?
There are a number of advantages for companies. Firstly, human and financial resource gains with pooled audits via yearly sampling. It also boosts agility as it’s easier to integrate a new site and the transfer of another does not destabilize the entire structure. Finally, centralized reporting improves the management and smooth deployment of the strategic priorities.
Who does this involve?
Potentially all companies with multiple locations, offices or production units, or those certified for multiple standards. This naturally brings industry and mid-cap companies to mind. The automotive and aeronautical sectors have been the first to take the plunge. But the tertiary sector also has everything to play for: whether it’s a bank or car dealership, the same standards should apply, whatever the city. And we mustn’t forget big groups. Let’s take Alstom Transport. In four years, the group and its one hundred locations have shifted from site-to-site certification to a global solution with our assistance.
What are your tips for success?
This is a very ambitious company project which must be supported by committed management and widely shared with teams. Without their support, success is impossible. Clean breaks should be avoided. Instead, companies should opt for a transitional plan while setting a limit – a target launch year!